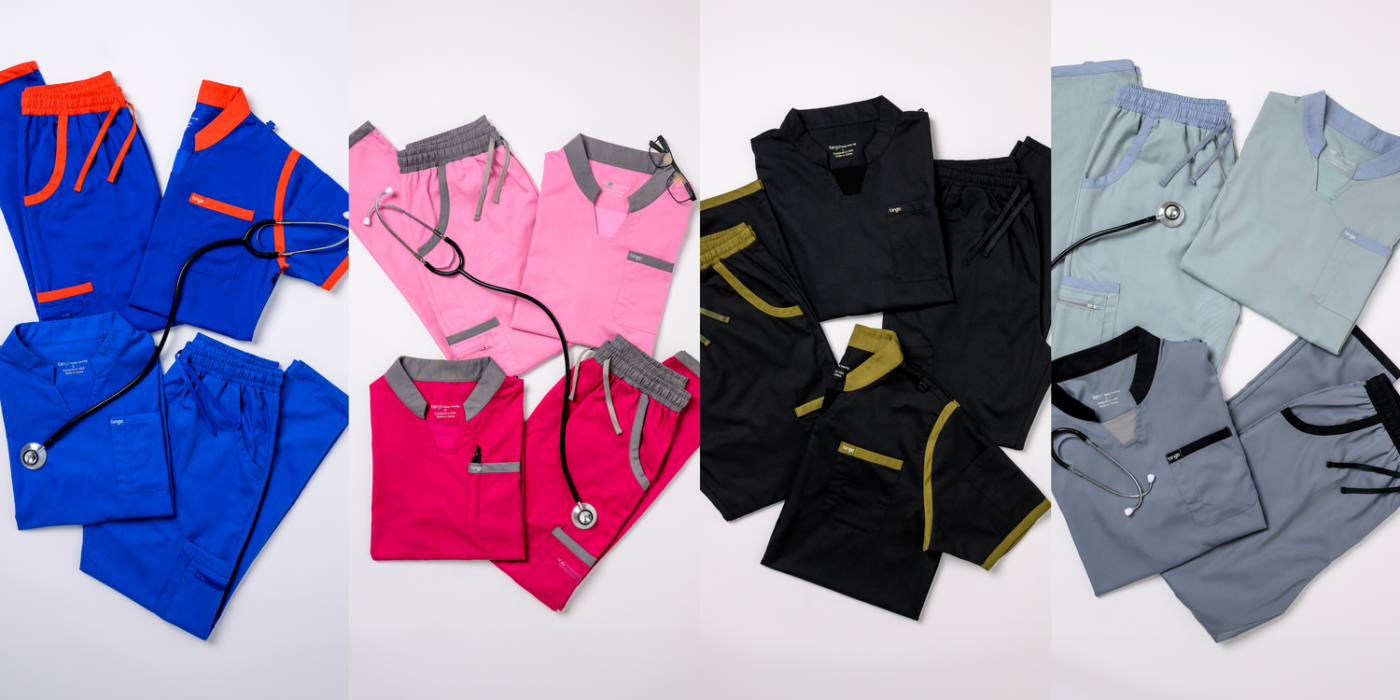
What Makes a Great Cut and Sew Product and How to Get Started: The Development of Tango Scrubs
Developing a successful cut and sew product involves a detailed process that spans understanding market needs, selecting the right materials, designing with purpose, prototyping rigorously, and efficiently managing manufacturing and sourcing. In this blog post, we’ll explore these five key themes through the development of Tango scrubs, a stylish and functional alternative to traditional doctors’ scrubs. This detailed breakdown will provide insights into what makes a great cut and sew product and how you can embark on developing your own.
1. Understanding Market Needs and Setting Clear Goals
The first step in developing any successful cut and sew product is to thoroughly understand the market needs and set clear, achievable goals. For Tango scrubs, the primary objective was to address the discomfort and lack of style in traditional medical scrubs.
We started with extensive research to pinpoint the specific pain points experienced by healthcare professionals. Surveys and interviews revealed common complaints about poor fit, lack of breathability, and insufficient functionality in existing scrubs. Additionally, there was a clear desire for more stylish options that would allow medical professionals to feel confident and look good while on duty.
Armed with this information, we set out with a clear goal: to create a set of scrubs that offered superior comfort, enhanced functionality, and modern aesthetics. This goal directed all subsequent design and development efforts, ensuring that every decision made was aligned with meeting these user needs.
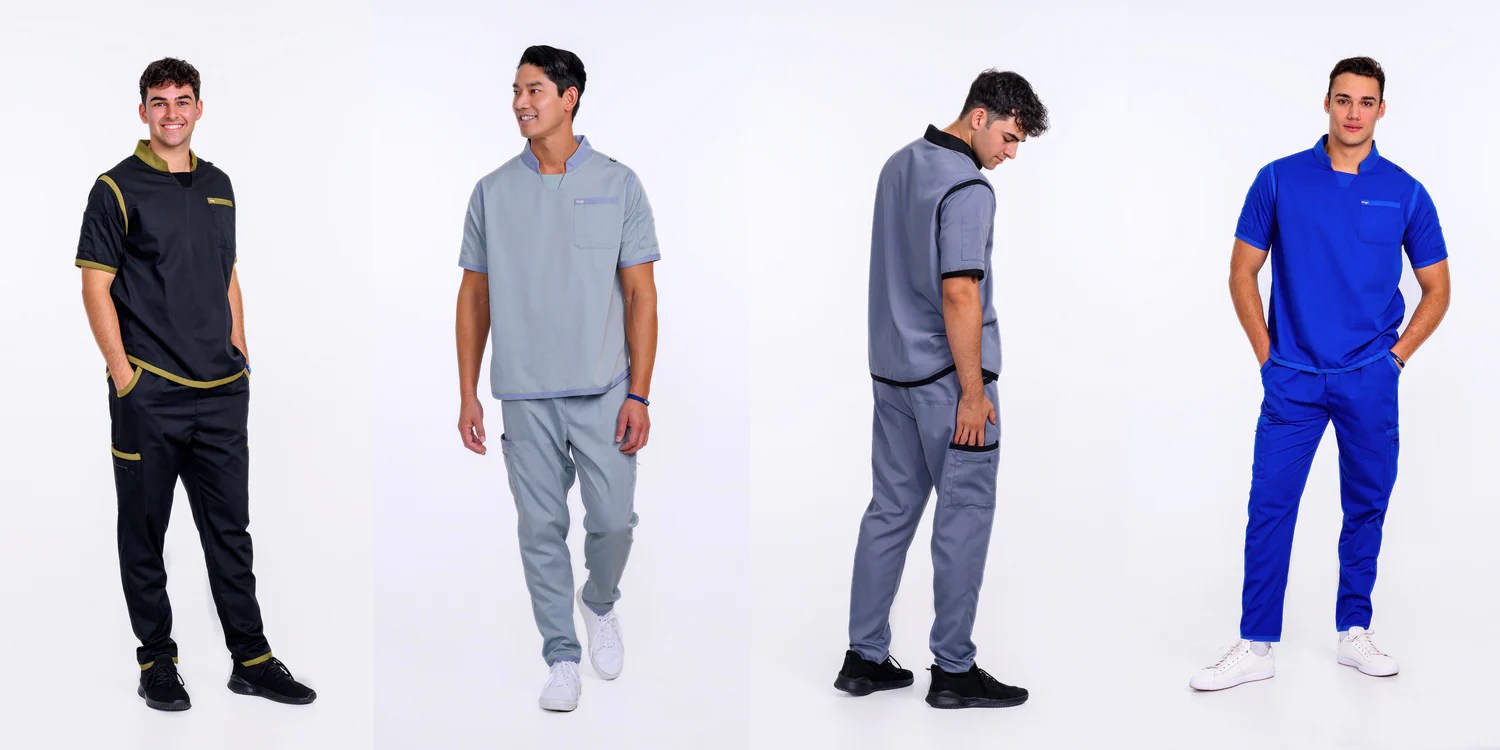
2. Material Selection and Fabric Innovation
Choosing the right materials is critical in the development of cut and sew products. The fabric must not only look good but also meet the specific performance requirements of the end-users. For Tango scrubs, finding the perfect fabric blend was a top priority.
Traditional scrubs often use basic cotton blends, which, while durable, fall short in terms of comfort and flexibility. To improve on this, we explored various fabric options and ultimately chose a blend of high-quality cotton, polyester, and spandex. This combination offered the softness of cotton, the durability and wrinkle-resistance of polyester, and the flexibility and stretch of spandex.
Beyond the basic properties of comfort and durability, we integrated advanced fabric technologies. Moisture-wicking properties were added to keep the wearer cool and dry, even during long shifts. Antimicrobial treatments were also applied to maintain hygiene, an essential feature in medical environments.
The careful selection and innovation in fabric ensured that Tango scrubs were not only stylish but also highly functional and comfortable, meeting all the necessary criteria for a great cut and sew product.
3. Purposeful Design and Aesthetic Appeal
Design is a crucial aspect that sets a great cut and sew product apart. For Tango scrubs, the challenge was to create a design that balanced functionality with aesthetic appeal.
Our professional design team collaborated with healthcare professionals to develop a design that was both practical and stylish. Key design features included strategically placed pockets for easy access to tools and personal items, various neckline and sleeve options to cater to different preferences, and a modern fit that allowed for ease of movement without compromising on a professional appearance.
Color and style were also major considerations. Traditional scrubs are often available in limited, monotonous colors. Tango scrubs introduced a broader palette, allowing healthcare professionals to express their personal style while adhering to workplace dress codes. Subtle design details like contrasting stitching and branded tags were added to enhance the overall look.
By focusing on purposeful design and aesthetic appeal, we ensured that Tango scrubs stood out in the market, providing a stylish and functional alternative to traditional options.
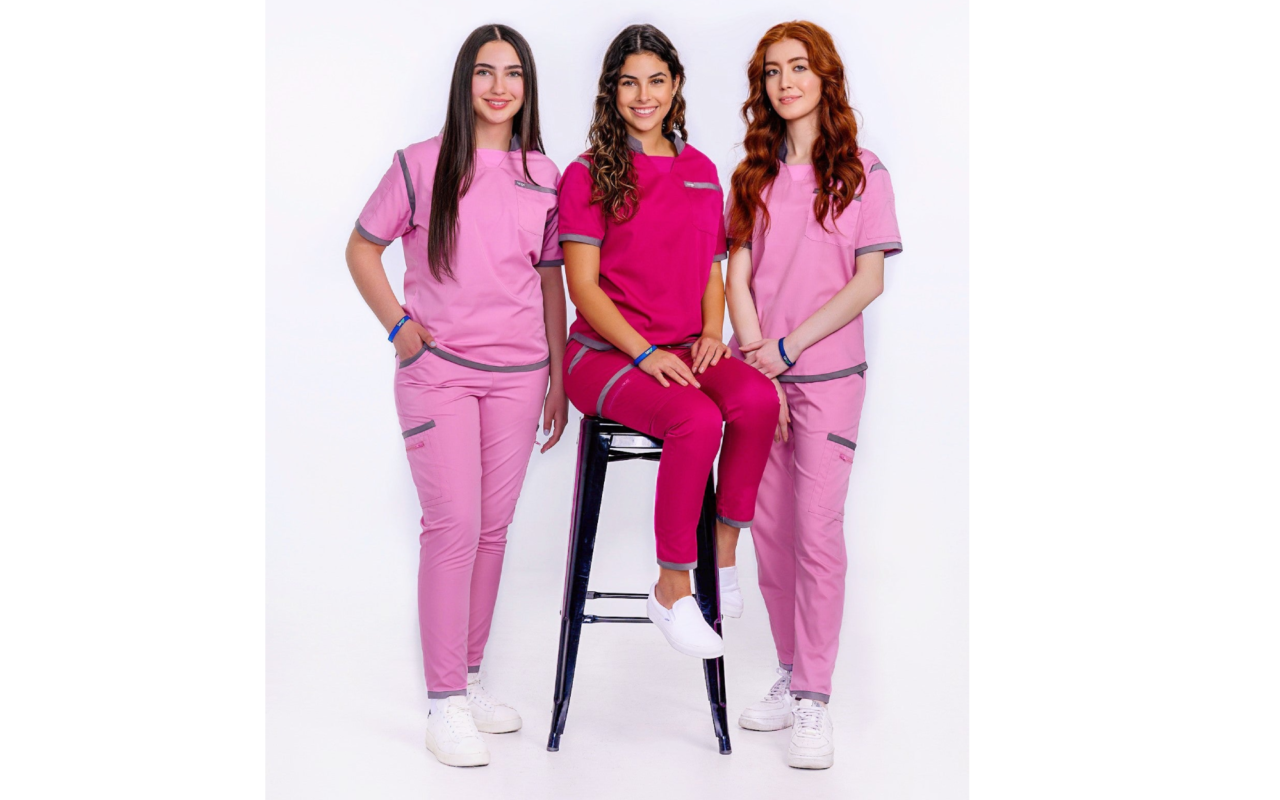
4. Prototyping and Iterative Testing
The prototyping phase is where the design concepts are transformed into tangible products. For Tango scrubs, multiple prototypes were created and tested extensively to ensure they met the desired standards of fit, comfort, and functionality.
Our clients played a pivotal role during the testing phase. We worked closely with them to gather detailed feedback and insights. Initial prototypes focused on the overall fit and material performance. Clients evaluated these early versions, providing valuable feedback on the scrubs’ comfort, practicality, and aesthetics. This feedback was instrumental in making continuous improvements.
Based on client feedback, adjustments were made to refine the design. This iterative process ensured that the final product was perfectly aligned with the clients’ expectations and the market needs. By involving clients closely in the prototyping phase, we were able to address any issues promptly and optimize every detail, from pocket placement to fabric stretch.
Durability was another key focus during testing. The scrubs needed to withstand the rigors of daily use and frequent washing. Reinforced stitching and stress points were incorporated to enhance durability, ensuring that the scrubs remained in excellent condition over time.
This client-centric approach to prototyping not only helped us refine the product but also ensured that the final Tango scrubs were tailored to meet the specific needs and preferences of healthcare professionals.
5. Efficient Manufacturing and Sourcing
With the final design and materials confirmed, the next crucial step was manufacturing and sourcing. Ensuring high-quality manufacturing processes was vital to maintaining the standards set during the development phase. The production process was meticulously planned to guarantee consistency and quality in every batch of Tango scrubs.
A significant advantage in this phase was our extensive network of manufacturing partners. This expansive resource made it easier to identify and collaborate with factories that could meet our stringent quality and performance standards. Leveraging these established relationships, we were able to quickly find the right factory that not only understood our requirements but also had a proven track record in producing high-quality garments.
By tapping into this network, we were able to negotiate the best possible pricing for our clients. Our ability to source competitively priced materials and manufacturing services without compromising on quality ensured that the production costs were kept manageable. This efficiency translated into cost savings for our clients, making the upscale Tango scrubs economically feasible.
The selected factory was carefully vetted to ensure they adhered to our rigorous quality control measures. This included thorough inspections of raw materials upon arrival, regular checks during the various stages of production, and final inspections of the completed scrubs. Each pair of scrubs underwent scrutiny for stitching quality, fabric consistency, and overall finish to ensure they met the high standards expected by healthcare professionals.
Exceptional communication and a fast timeline were integral to the sourcing and manufacturing process. Our team maintained constant communication with the factory to monitor progress and address any issues promptly. This proactive approach ensured that the production stayed on schedule and met all deadlines. The efficiency of this process allowed us to bring Tango scrubs to market swiftly, meeting the urgent needs of healthcare professionals.
By focusing on high-quality materials, maintaining rigorous quality control, and leveraging our extensive network of manufacturing partners, Tango scrubs achieved a standard of excellence that met the demanding needs of healthcare professionals. This commitment to quality ensured that every pair of scrubs not only looked stylish and felt comfortable but also stood up to the rigors of daily use in medical environments.
Lime Design's Approach to Perfecting Product Development

In the realm of product development, there is an art to embracing failure as a catalyst for growth and improvement. Lime Design, a leading product development firm, has mastered the art of failing forward, using it as a powerful tool to uncover and refine imperfections in the journey of bringing an inventor’s idea to life. By understanding the value of iteration and actively seeking out failures, Lime Design’s team is able to transform setbacks into stepping stones towards creating exceptional products. In this blog, we delve into Lime Design’s unique approach and how they harness the art of failing forward to perfect the development process.
Unlock your product’s potential with our help! Avoid the headaches of product development. Let our team handle the tough parts while you focus on your vision. Contact us now to start building your future!